Hoy en día, las industrias cuentan con una gran variedad de equipos, cada uno, con características propias.
Por tanto, resulta poco justificable, el uso de un mismo tipo de mantenimiento (correctivo, preventivo, otros), para todos los equipos de una planta o instalación.
Si se desea optimizar, los planes de mantenimiento de los equipos, se deben considerar una serie de factores.
Algunos de estos factores son: costo de parada de producción, impacto en la seguridad, costo de reparación.
En fin, se debe identificar cuáles son las tareas de mantenimiento más convenientes para cada maquinaria.
Es por ello, que se requiere desarrollar un trabajo previo, a la elaboración de un Plan de Mantenimiento.
Diagnóstico de la Situación Actual
Inspección Técnica
En primer lugar, se debe estudiar cada uno de los equipos que constituyen la instalación, determinando con cierto nivel de detalle, cuáles son las tareas rentables y cuáles no lo son.
De ese modo, en una planta que posea cientos o miles de equipos, este trabajo puede parecer inmenso e interminable, pero no es así.
Por lo general un estudio diagnóstico puede representar entre uno o dos meses dependiendo de la formación del personal técnico.
Elección de la Modalidad de Mantenimiento
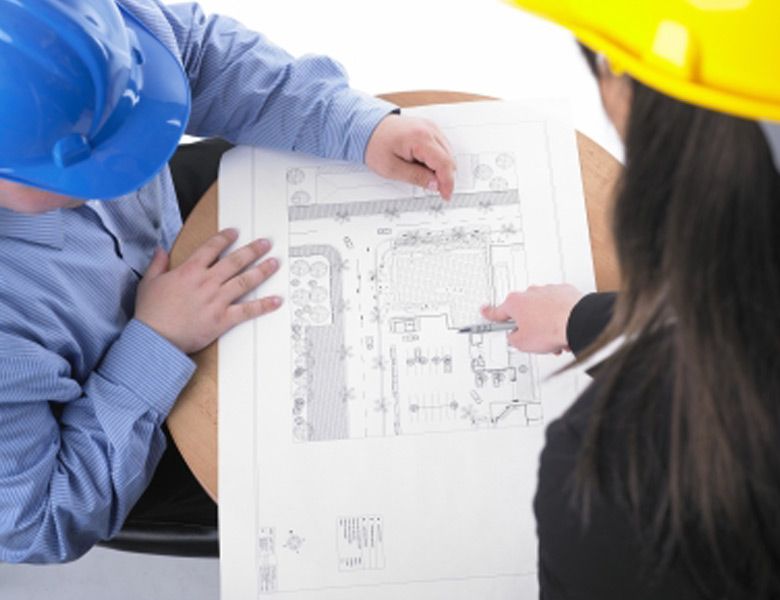
Especificaciones del Fabricante
Para elaborar un plan de mantenimiento industrial, se deben tomar en cuenta las siguientes modalidades:
1. Indicaciones de los fabricantes, tomando en cuenta los aportes de los técnicos de mantenimiento de la planta.
2. Protocolos (instrucciones genéricas) de mantenimiento por equipo, validando los planes definitivos con el personal de mantenimiento de la empresa cliente.
3. Análisis de fallas potenciales de la instalación, y determinación de medidas preventivas que eviten estas fallas. Esta metodología también es conocida como Mantenimiento Centrado en Confiabilidad (MCC).
¿Cómo saber cuál de las 3 modalidades implementar?
Si no existe un historial de mantenimiento previo
En instalaciones que no cuentan con un plan de mantenimiento, resulta adecuado iniciar con algo sencillo y ponerlo en marcha.
Eso se puede hacer siguiendo las especificaciones de los fabricantes o con base en instrucciones genéricas (protocolos), y en la experiencia propia o de otros.
Si se dispone de un sólido conocimiento de los equipos
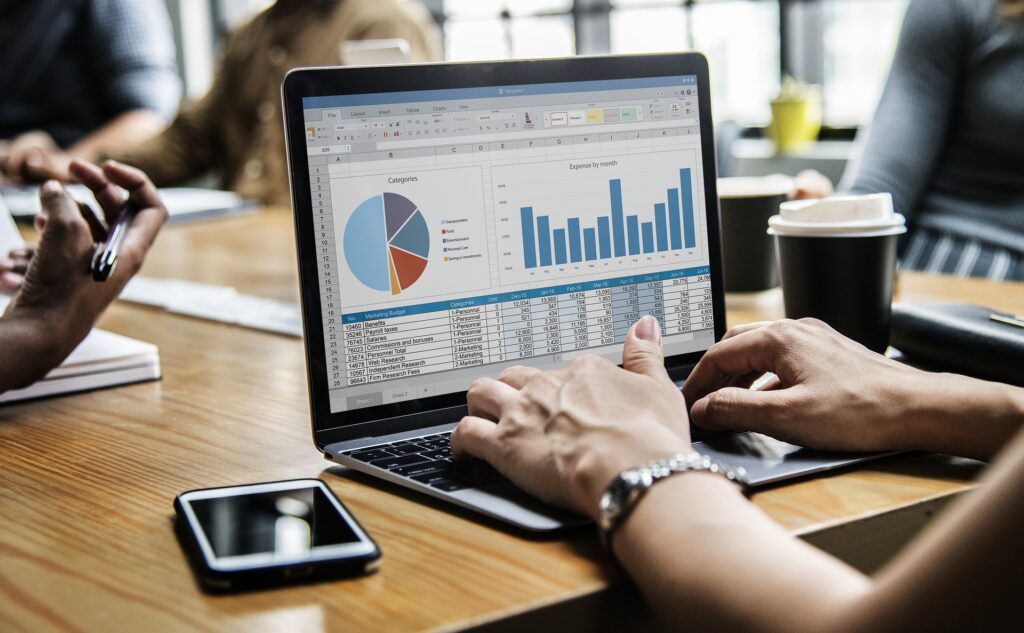
El historial de fallas es clave
Por otra parte, el plan de Mantenimiento Centrado en Confiablidad, es aplicable en instalaciones que presentan algún avance en materia de gestión de mantenimiento.
Esto se debe, a que se requiere contar con información sólida acerca de los equipos, generando resultados excelentes, como lo son, el aumento en la disponibilidad de la planta, y la reducción de los costos de mantenimiento.
¿Resulta necesario invertir en un Plan de Mantenimiento para su Instalación?
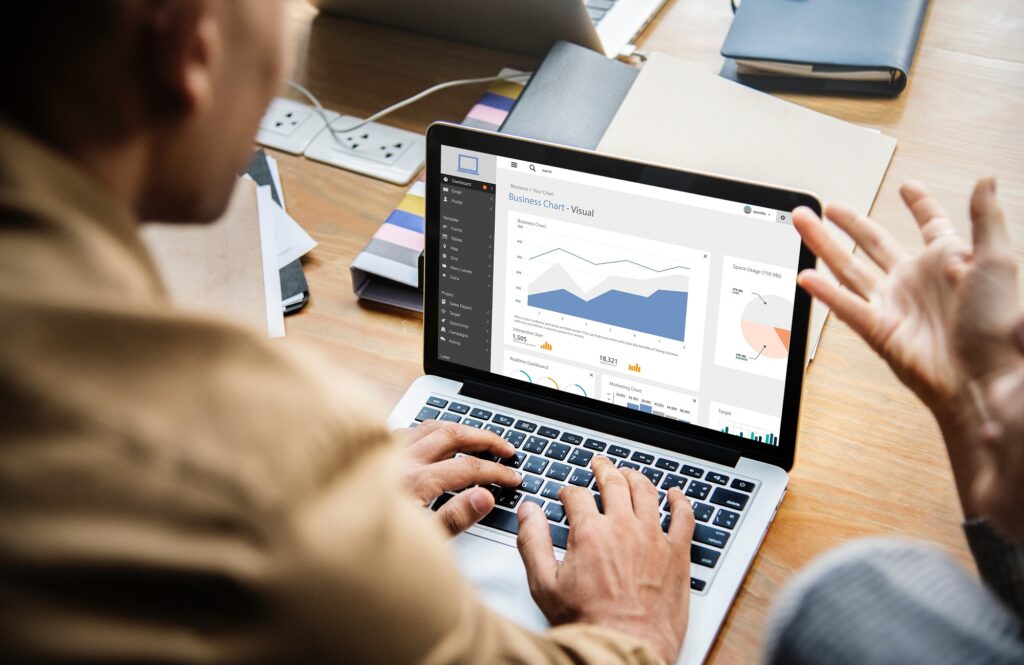
Si se entiende que los efectos más comunes de no hacerlo, se traducen en baja productividad y pérdidas económicas, se obtendrá una respuesta automática. Estos son algunos de esos efectos:
– Desperdicios por averías, lo que genera pérdidas de tiempo, defectos de calidad y re-trabajos, pérdidas de clientes, impacto negativo en la imagen de la empresa.
– Pérdidas por paros inesperados, que se generan por mal operación de la máquina.
– Pérdidas por velocidad reducida, debido a bajo rendimiento en la operación de los equipos.
En Resilio, C.A., le apoyamos en el proceso de elaborar planes de mantenimiento que se ajusten a la realidad de su organización.
Nosotros nos ocuparemos de guiarle de un modo sencillo, práctico y profesional.
Resulta clave, contar con un personal empoderado y formado, para que esté en capacidad de hacer seguimiento a la mejora continua del plan.
Su retribución será el incremento notable de la productividad, rentabilidad y competitividad de su empresa.
Una de esas ventajas, es que permite al contratante centrarse en su negocio principal, y dejar en manos de especialistas, todas las tareas que giren alrededor de su producto o servicio.